Safety measures are important when operating machine tools to ensure the safety of workers. With advanced technology, various advanced safety solutions such as automatic doors, cable carriers, protective covers, and pit covers contribute to safer operations in machine tools. This blog discusses how these advanced safety solutions lead to safer and more efficient machine tool operations.
Automatic Doors
Opened grinded machine tools consume more energy by over 75 percent, which leads to higher utility bills. As a result, it is essential to shut off the grinded machine tools when they are not used; thus, operators are advised to detach from the power sources when not in use completely. The use of automatic doors on the machine tools allows operators to access the machine tools easily without necessarily wasting time opening the covers. Machine tools cover large plugs, bonnets, and do-not-have-holes-in-the-firewall machines and physical devices that reduce the risks of fire outbreaks.
Automatic doors are barriers placed when the machines are not in use to avoid the accumulation of contaminators between the machine tools. When the covered machines are turned on during machine tool operations, the grinded powder present in the closed grinded machine tools might explode, eventually causing equipment damage. The Innovative Safety Solutions for Machine Tools offer protection to the machine operators.
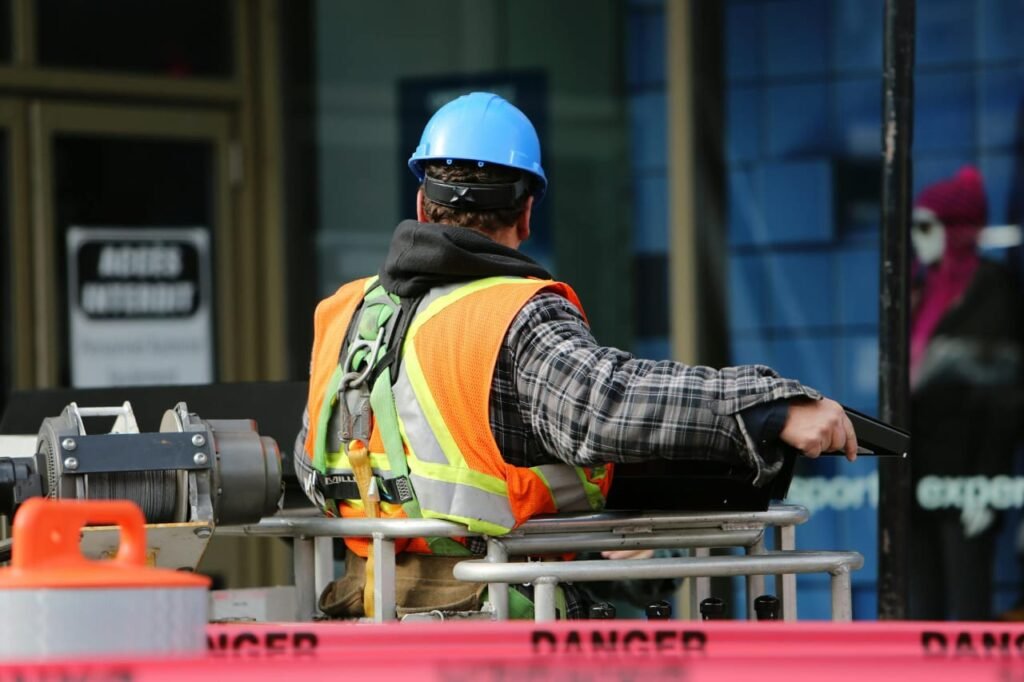
Cable Carriers
Machine tools such as lathes depend on the cables from the power transmitting systems and computer systems, and they should feed smoothly without snugs. Poor feeding can cause the system from which the machine tool depends to black out or trip.
Cable carry is essential to prevent the industry’s main system since it enables the smooth running of the power from the source to the machine without a circuit break.
When cables are pulled and pushed on the floor of the production hall in a trial-and-error method, the productivity of the company reduces since they divert the attention of the managers and fixers.
In most of the workbenches’, automated guided vehicles are used to supply lathe from the workstation.
The bending and moving robotic vehicles that carry lathe machines introduce the challenge of ensuring that cable carriers are installed to allow smooth feeding of the lathe.
In chain flex, turquoise and turgid go modeling have been used to analyze and identify flexible cables in the cable carriers as guides for machine movement.
Pit Covers
Lathes and milling machines are computerized machines manufactured using technology that reduces human labor and effort required in coupled manufacturing companies. They run in a numeric control system that enables manufacturing mass production of work pieces that grade the components of the lathe and milling machine tool system.
Pit covers are safety measures placed on the booth of the lather. They enable an operator to run the procedures of the machine lathe with minimal risks. Reviewing examples of risk assessments in the industry, lathes, and pit machines require the highest level of pit cover to eliminate the risk that may be brought about by sharp turning tools. Pit covers from Dynatect contribute to safer and more efficient machine tool operations
Advanced safety measures are crucial in machine tools since their environment is hazardous, and most of them are made of heavy metals that need to be monitored.